With decades of automation expertise, Clevertech delivers fully integrated, customizable solutions to streamline production and enhance efficiency for wineries across North America.
The family-owned business is one of the hallmarks of the wine industry. These are the oldest type of commercial organization. Studies have found that they are more likely to thrive, in part because they approach business from a legacy perspective. One of the reasons for this success is the inherent multi-generational focus.
“The family legacy matters,” says Beth Zarnick-Duffy, who has worked with many family-owned wineries in her 30-year career and is now a sales manager for Clevertech North America (NA). “It’s more personal, more about relationship building.”
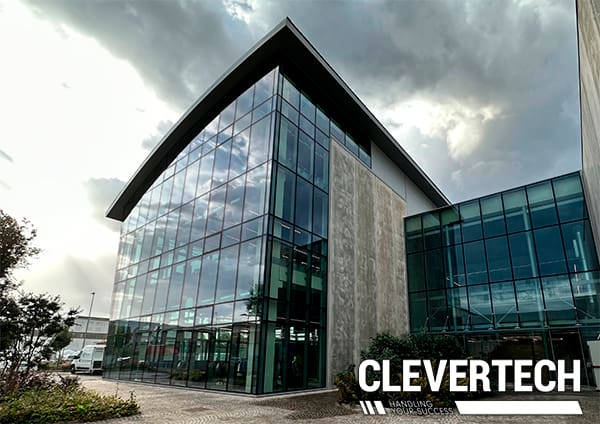
“I agree. It’s a big plus,” says Giorgio Zanardi, Clevertech NA’s General Manager. “Our parent company, Clevertech SPA, is a family-owned company. That means when we do business with our customers, it’s not just about business and profits. It’s about building a partnership with them that lasts years. Our clients have a direct relationship with us here in North America, but, of course, the owner of Clevertech SPA in Italy is also involved. I can tell you he has direct conversations with our customers.“
Holistic and fully integrated solutions
Since its founding in 1987, the Italian company has become a leader in the automation sector, designing and manufacturing depalletizers, palletizers, case packers, partition inserters, carton erectors, and fully integrated handling systems for a wide variety of industries, including home care, personal care, petfood, container manufactures, beverage, and in the last 2-3 years, wine and spirits. It provides its holistic and fully integrated engineering solutions to the world’s largest producers of consumer goods, including Procter & Gamble, Henkel, Clorox, Smucker’s, Folgers, and Kroger.
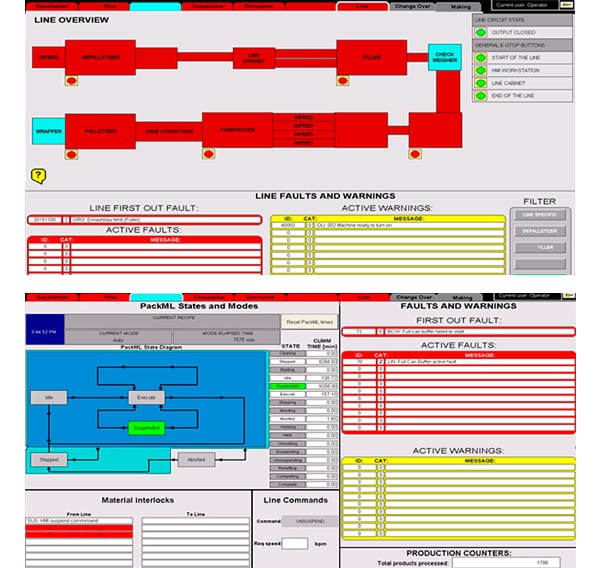
Clevertech has brought its experience with developing highly customized solutions for these companies to the wine industry, along with our robotic and traditional pals and depals at high or low level. These engineering solutions are fully integrated so that every piece of technology has standardized mechanical and electrical design and components. The machines also share a software language, Pack ML, with a library of programming code modules that are reused across the machines, making it faster to program and increasing reliability.
“This full integration is our signature,” says Zanardi, who has over 18 years of experience in the industrial packaging equipment business. “We are the only company capable of delivering a fully integrated system to the wine market.”
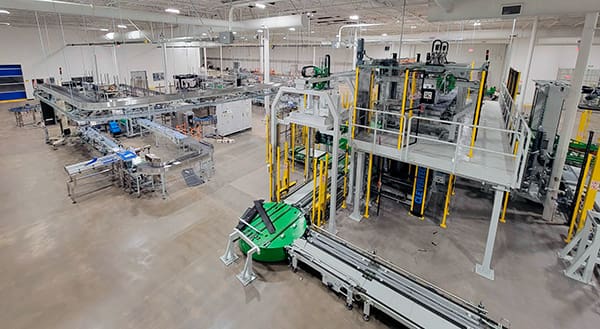
Having the same design throughout translates to a higher line and operator efficiency. Operator training on one machine in the line means immediate familiarity with all modules. As they move from screen to screen, they see the same schematics, format and alarms. This level of standardization minimizes downtime and boosts efficiency. Clevertech’s gold-standard approach to full line integration distinguishes it from companies that merely integrate machines without this level of consistency.
These fully integrated systems align with the design guidelines of TPM (Total Productive Maintenance), a holistic approach to maintenance that gives the operator a full view of each machine and its components. They can stand outside the machine safety area and visually detect and troubleshoot any problems that arise much more quickly, thus reducing downtime and recovery time.
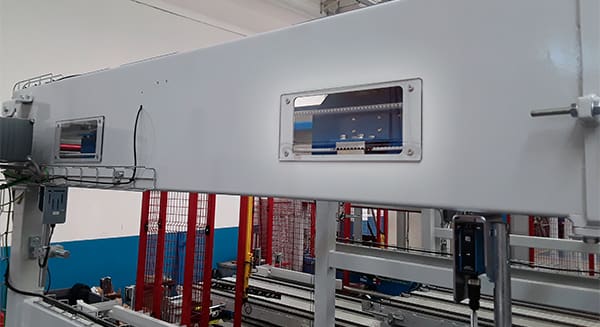
Design and Testing
Clevertech’s unique modular design allows it to configure each line to match the customer’s space and functionality requirements. This customization through standardization allows Clevertech to tailor the machines and layout without requiring a complete redesign. It makes options like a compact system that can depalletize empty glass and palletize cases from two different lines.
Zanardi points out, “We’re bringing advantages we’ve learned in other markets to the wine industry.” He offers the example of being the first to bring a particular type of VAT/ FAT (Factory Acceptance Testing) from the food industry to the wine industry. Clevertech’s different approach to FAT ensures that everything Clevertech sells is thoroughly tested and fully assembled at its facility and invites the customer to see all their equipment from the line fully assembled and running that the same production speed it would be in their facility, prior to preparation for delivery. That means a vertical start up on site; reassembly, commissioning and startup at the customer site is much faster, which saves the winery time and money. Another innovation is doing a complete simulation of a one-of-a-kind project or a new application that is in the conceptual stage to ensure a new idea will work—even before it is sold. Proof in the concept!
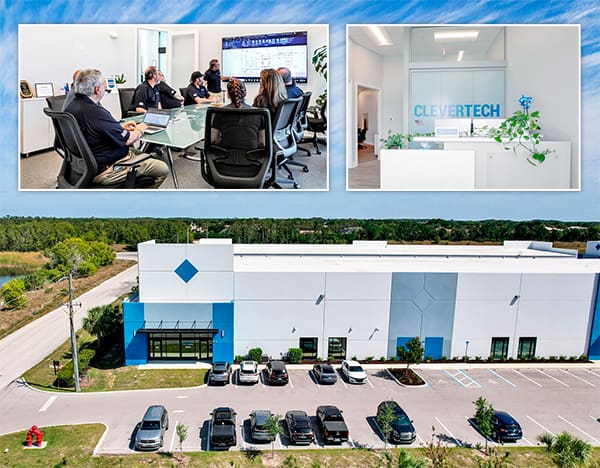
Clevertech’s North American headquarters are in a 29,000 sq ft facility in Fort Myers, Florida, where it hosts an aftermarket team, a team of 50 engineers and technicians, a warehouse of spare parts and 24/7 support that is backed by Clevertech’s eight worldwide subsidiaries. The Florida team regularly travels to customers on preventative maintenance schedules or to do periodic audits.
“It’s really critical that our customers know Clevertech North America is their first point of response,” says Zarnick-Duffy, “and if they call us, someone will pick up the phone any time of the day or night, listen to the problem and walk them through how to get their system up and running. If it can’t be done remotely, we’ll send someone to fix it.”
To learn more about Clevertech’s automation & equipment solutions, visit their website or contact Beth directly at or b.zarnick@clevertech-group.com
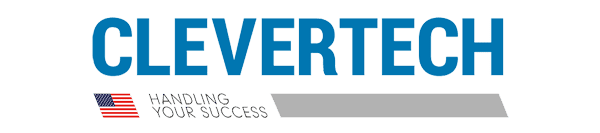